The dimensions of a box are more than just numbers; they’re the foundation of a product’s safety, cost-efficiency, and overall presentation. While measuring a box might seem like a simple task, ensuring accuracy is paramount, especially when it comes to custom packaging. Let’s dive into the nuances of measuring box dimensions and why it’s so crucial for your business.
Understanding Length, Width, and Depth
Before you even think about manufacturing, it’s essential to grasp the three primary dimensions of any box: length, width, and depth. Here’s a quick breakdown:
Length
The longest side when viewed from the top.
The length of a box is typically its longest side when viewed from the top a.k.a the opening. It serves as the primary dimension that often determines the orientation of the box. In many cases, the length corresponds to the horizontal dimension of the product inside, especially for elongated items. When measuring the length, it’s essential to start from one end and extend the measuring tape straight across to the opposite end, ensuring it’s taut and level.
Key Point: The length is crucial in determining the orientation of the box and often corresponds to the primary dimension of the product inside.
Width
The shorter side when viewed from the top.
The width of a box is the shorter side when looking at the top. It’s perpendicular to the length and often determines the front face of the box, especially in display packaging. When measuring the width, ensure that the measuring tape spans from one side to the other without any slack. It’s also worth noting that the width can vary based on the design of the box, especially if it has unique shapes or cutouts.
Key Point: The width is vital for display purposes and can influence how a product is showcased on retail shelves.
Depth (or Height)
The side perpendicular to both length and width.
Depth, interchangeably referred to as height, is the side perpendicular to both the length and width. It determines how tall the box stands. For products that are stacked or need to fit within specific storage constraints, the depth is a critical measurement. In the case of a shoebox, for example, the depth would accommodate the height of the shoe boxes stacked on top of each other. Measuring the depth requires a vertical measurement from the base of the box to its topmost point. For boxes with lids or flaps, measure the depth including the flaps as they reduce the usable internal dimensions.
Key Point: Depth is crucial for understanding how products will be stacked or stored, ensuring efficient use of space.
Volume: More Than Just Space
Once you’ve got your three dimensions, it’s time to calculate the volume. This isn’t just about how much space is inside the box; it’s about optimizing material use, reducing costs, and ensuring the structural integrity of your custom packaging.
Calculating Volume
To calculate the volume, use the simple formula: Volume = Length x Width x Depth. While it’s technically possible to calculate volume without knowing which measurement is which, it’s a good practice to keep them straight to avoid confusion.
Pro tip: Measure each dimension at 3 different spots for accuracy.
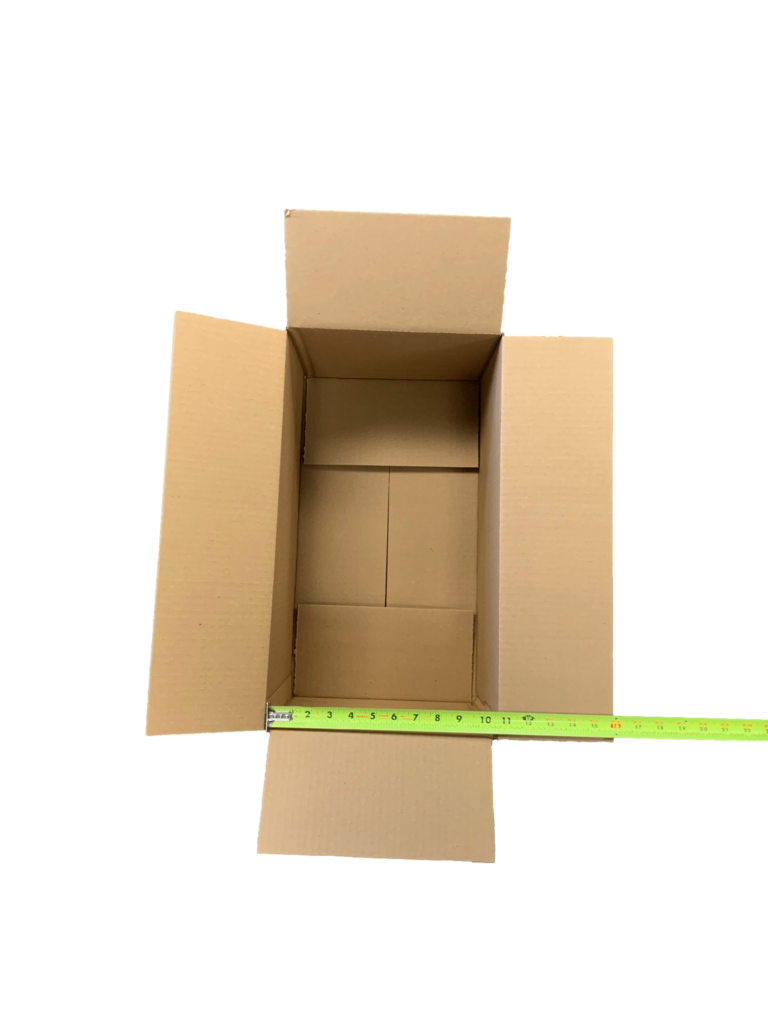
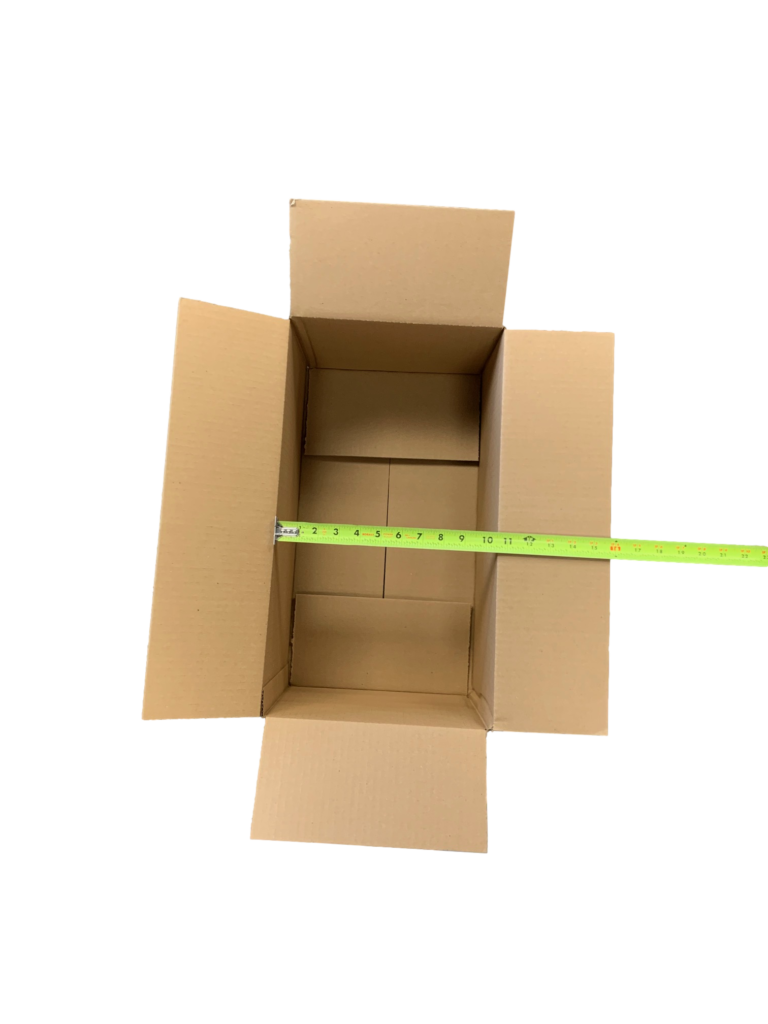
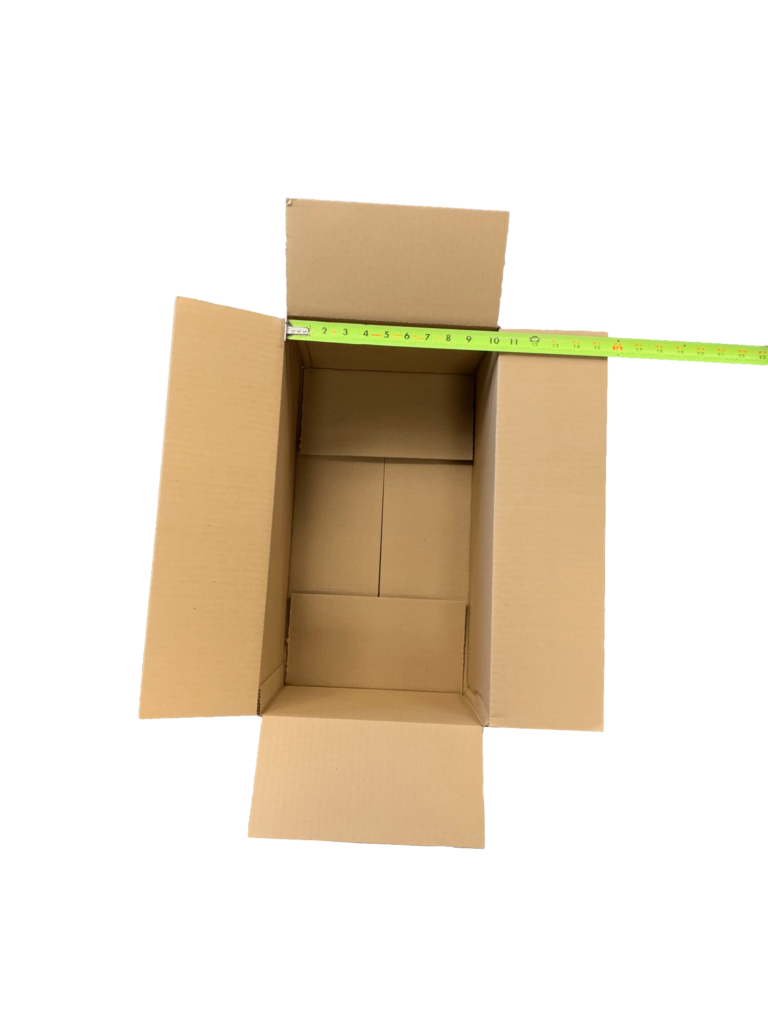
Why Volume Matters
Optimal Product Fit: The volume of a box determines how snugly a product will fit inside. A box with the right volume ensures that the product is well protected and displayed optimally and aesthetically when unboxed.
Material Efficiency: Knowing the volume helps in selecting the right amount of protective packaging material, reducing waste and costs. Overestimating volume can lead to unnecessary material costs, while underestimating can compromise the product’s safety.
Shipping and Warehousing: Carriers often charge based on the volume (or dimensional weight) of packages. A box with optimized volume can lead to significant savings in shipping costs. Additionally, understanding volume aids in efficient warehousing, allowing for better stacking and storage. Pax Solutions can help you in understanding efficient warehousing and pallet optimization.
The Inside Story: Why Internal Dimensions Matter
Here’s a pro tip: always measure the inside of the box, not the outside. Why? Because the industry standard is based on internal measurements. This distinction is crucial for ensuring that your product fits snugly and securely inside its custom packaging.
The Importance of Internal Measurements
Measuring the external box dimensions might seem easier, but it doesn’t account for the thickness of the box material. This can be especially misleading with corrugated boxes, where the fluting adds extra millimeters to every external measurement. Visit our packaging resources page for charts and further education on material thicknesses.
Precision is Key
Measuring box dimensions might not be rocket science, but it demands attention to detail. Whether you’re calculating volume or deciding between internal and external measurements, accuracy is crucial. With these insights, you’re well-equipped to tackle any packaging project. And if you ever need expert guidance, remember that professional help is just a click away. PAX Solutions would love to help bring your vision to life.